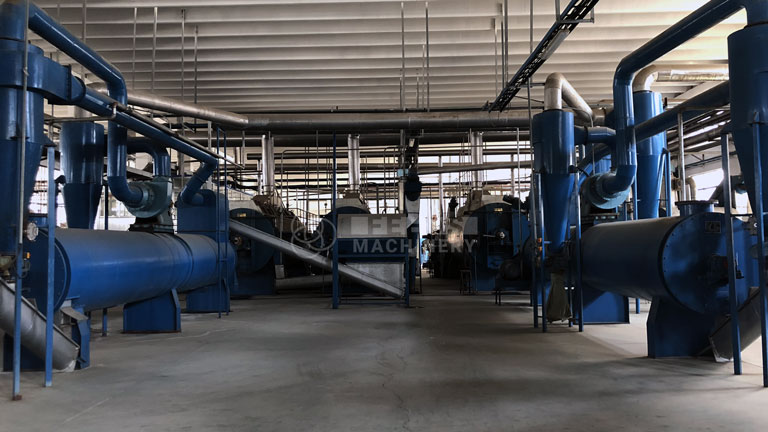
Building a involves careful planning, proper equipment selection, and understanding the fish meal production process. Whether you’re entering the fishmeal industry or expanding your production capacity, knowing how to set up a fish meal plant efficiently is crucial to success.
In this guide, we’ll walk you through the essential steps for building a fish meal plant, from the initial planning phase to the final setup. We’ll also cover key considerations, equipment requirements, and best practices to ensure you get the most out of your investment.
Step 1: Conduct Feasibility Study
Before you start building a fish meal plant, it’s critical to conduct a feasibility study. This study should analyze the market demand for fishmeal, the availability of raw materials (such as fish by-products), and local regulations. You will also need to determine the scale of your plant based on projected production volume and operational capacity.
Key Considerations:
- Market Research: Determine the demand for fish meal in your target markets.
- Raw Material Availability: Secure a consistent supply of fish by-products.
- Regulatory Requirements: Understand local environmental and operational regulations for fishmeal production.
Step 2: Design the Plant Layout
Once you’ve completed the feasibility study, the next step is designing the plant layout. An efficient layout can reduce operational costs, streamline production, and ensure compliance with safety and environmental standards. This layout should include the raw material reception area, processing zone, drying and grinding section, storage, and packaging.
Key Considerations:
- Space Optimization: Plan an efficient flow from raw material reception to final packaging.
- Waste Management: Include facilities for treating wastewater and waste gases to reduce pollution.
- Safety: Design the plant to adhere to health and safety standards for workers.
Step 3: Select Equipment for the Fish Meal Plant
The most important aspect of building a fish meal plant is selecting the right equipment. The main stages of the fish meal production process include cooking, pressing, drying, and grinding. Each of these steps requires specialized machinery to ensure efficiency and quality. Here’s a breakdown of the equipment you’ll need:
- Fish Cooker: Used to steam the raw fish, breaking down proteins and separating oil and water.
- Screw Press: Extracts liquid (fish oil and water) from the cooked material, leaving behind press cake.
- Disc Dryer: Reduces moisture content in the press cake to produce dry fish meal.
- Grinder: Grinds the dried fish meal into a fine powder for packaging.
Make sure to select high-quality, energy-efficient equipment to minimize operational costs and increase productivity.
Step 4: Construction and Installation
After designing the plant layout and selecting the necessary equipment, the next phase is construction and installation. Work with experienced contractors to ensure that the building meets all structural and safety standards. Once the facility is ready, install the equipment in accordance with the plant design.
Installation Tips:
- Ensure that all equipment is properly aligned and secured for optimal operation.
- Work with your equipment supplier to conduct initial testing and calibration.
- Provide training for your staff on the correct operation and maintenance of the equipment.
Step 5: Test and Commission the Plant
Before starting full-scale production, you need to conduct a series of tests to ensure that everything runs smoothly. Testing and commissioning the plant involves running trial batches to check that all machinery is functioning properly and that production targets are achievable.
Key Considerations:
- Trial Production: Run a test batch to identify any potential issues in the production line.
- Adjustments: Fine-tune the machinery to optimize efficiency and output.
- Training: Ensure that staff are fully trained on safety protocols and equipment operation.
Step 6: Environmental and Waste Management
A well-designed fish meal plant should include systems to manage environmental impact. Wastewater and waste gases are by-products of the fish meal production process, and proper treatment systems are essential to avoid pollution.
Key Considerations:
- Wastewater Treatment: Install filtration and treatment systems to purify wastewater before discharge.
- Air Emissions: Implement air filtration systems to reduce harmful emissions and odors.
By addressing these factors, you’ll ensure your fish meal plant complies with environmental regulations and operates sustainably.
Step 7: Start Full Production
After successfully testing and commissioning the plant, you’re ready to begin full production. Keep a close eye on the production process during the initial weeks to ensure that everything operates smoothly. Regularly inspect the equipment and make any necessary adjustments.
Conclusion
Building a planta de farinha de peixe involves a detailed process, from feasibility studies and plant design to selecting the right equipment and ensuring efficient waste management. By following the steps outlined in this guide, you can set up a successful fish meal production line that meets your production goals and complies with regulatory standards.
Remember that proper planning and equipment selection are critical for ensuring a cost-effective and high-quality operation. Whether you are scaling up or starting fresh, understanding the fish meal production process will help you achieve long-term success in the industry.
Key Takeaways:
- Conduct a feasibility study to assess market demand and resource availability.
- Design an efficient plant layout to streamline production.
- Choose high-quality, energy-efficient equipment tailored to your production needs.
- Ensure proper waste management systems are in place for a sustainable operation.
- Train staff and perform regular equipment maintenance to maximize efficiency and product quality.